Work Order Software
Run and scale your service business effortlessly. Boost technician productivity, increase revenue, and simplify work order tracking with Bella FSM.
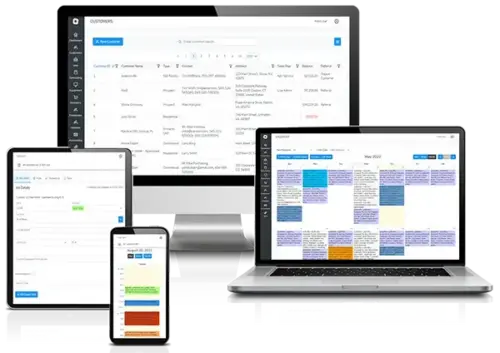
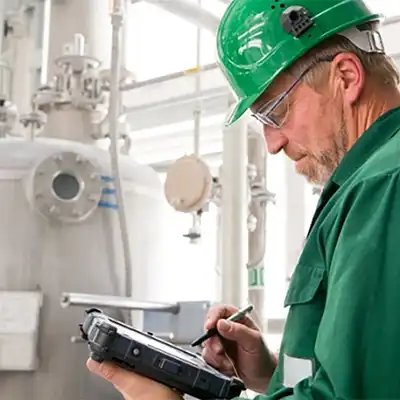
Eliminate paper which is inefficient and filled with errors
Enhance communication between the office and field teams
Your team will have all the data they need to complete the job right on the first visit
Build a stronger reputation by delivering exceptional customer service
Gain clearer insight and ensure greater accountability
Eliminate bottlenecks and boost efficiency for faster, more streamlined operations
Increase your revenue and boost profitability
Beneficial Features of our Work Order Management Software
Work Order Management
Easily track and manage work orders along with all related details - assignments, labor, expenses, materials, photos, and more. With powerful, flexible customization, we adapt to fit the way you work.
Preventive Maintenance
Recurring jobs make it easy to manage repeat tasks and preventive maintenance by automatically generating work orders at the intervals you choose. Email and text alerts keep you and you customers on the same page.
Asset Management
Stay on top of the assets and equipment you service by attaching before/after photos, user manuals, and more. Run detailed service history reports to spot maintenance trends and pinpoint problem areas.
CRM
Mobile Access from Anywhere
Signature Capture
The Importance of Work Order Software in Business Today
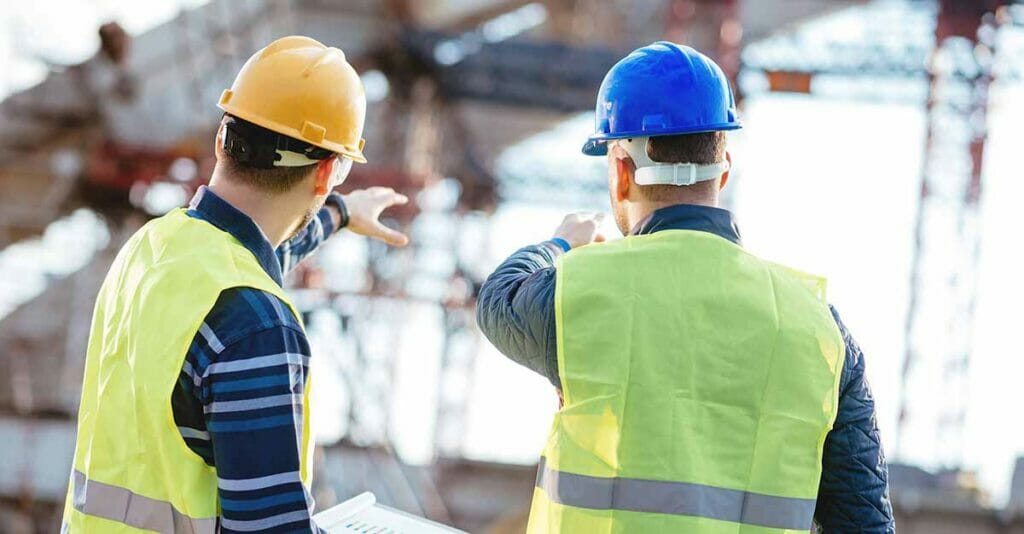
The best work order software for small business is more than just a digital tool. A transformative software program for managing tasks, tracking progress, and ensuring that operations run smoothly.
Its significance is immense, as it impacts every facet of operation management, from maintenance requests to project assignments.
In today's fast-paced environment, efficiency and organization are not just goals but necessities. Software for work order management helps companies streamline operations, manage tasks, and increase productivity in different sectors.
Work Order Maintenance Software
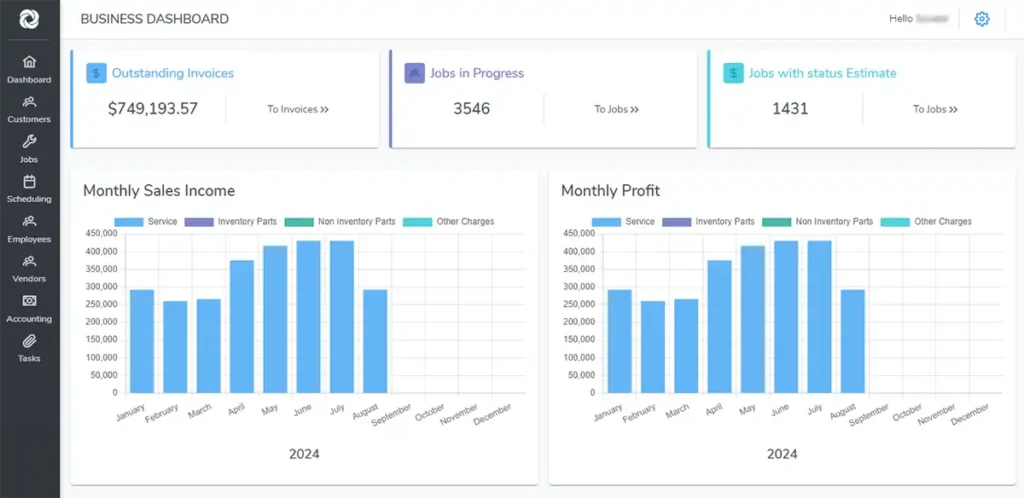
- Status tracking
- Service history
- Mobile app
- Customized forms
- Managing of inventory
- Real-time updates
- Track travel times
- Asset Management
- Preventive maintenance
- Maximize resource allocation
Get to the Next Level with Work Order Tracking Software
Companies save money and improve operations by choosing the right service technician work order software. We are the best work order management system for your business.
Steps of Field Service Work Order Management
Good work order software handles three main phases of the life cycle - creation, completion, and recording. Also, you can break down these phases into several steps.
To avoid having too many tasks at once, it's crucial to understand each step and have a dependable work order management process in place. This will help ensure that everything progresses smoothly and efficiently.
Having a clear understanding of the steps involved in a maintenance task can prevent them from becoming overwhelming. Also, reliable software can keep tasks organized and moving forward without any delays.
1. The task is identified
Tasks fall into two groups, planned and unplanned maintenance. Planned tasks are ones you know about beforehand, like routine inspections. Unplanned tasks are ones you can't predict, like unexpected breakdowns.
2. The request is created
The details are put together and submitted to the team for further action. For example, when a machine breaks down, requesters create a request and submit it. The software triggers at the proper time when planned.
3. Prioritize
Some requests are more critical than others. You don't need to fix a burnt-out light bulb right away, but you might need to fix a broken conveyor belt. That’s why you need to prioritize every task that hits your desk.
4. Time to schedule
Online work order software for small business assigns based on a set deadline, planned triggers, or dedicated blocks of time. Setting a deadline keeps everyone accountable and informed so nothing falls through the cracks.
5. Assigned and completed
Turn those words on a page into action, assign to a technician, who then completes the job. This can be a five-minute check of equipment, or it can be a complex repair that takes several days.
6. Closed and documented
7. Analyzed and/or modified
Closed status contains valuable information. Also, it offers insight into processes that you use to fine-tune operations. Keeping a log helps technicians and managers find missed steps or solutions if a problem happens again.
This article highlights the benefits of implementing work order management. It details how this program optimizes business operations, enhances customer service, and increases overall productivity. Key work order system features include scheduling and dispatch, parts and inventory management, facility management, customer communication and invoicing.
We designed the program for use on all mobile devices. It lets technicians check repair history, update job statuses and receive payments from the field.
By using work order scheduling software, business owners can make processes easier. They can lower costs and improve communication with customers. This helps to grow the business and increase profits.